Circular economy project brings seniors full circle
Lauren Smith
Apr 14, 2025

For chemical engineering seniors, the fall semester is defined by Chemical Process Systems Design. In the project-based course, student teams create a conceptual design and economic evaluation for a process to chemically recycle plastic.
It's the culmination of the technical knowledge, design approaches, and systems thinking that they've learned throughout the curriculum. "You learn all these core theories with fluids and thermodynamics and heat and mass. And then in this one class, you finally see everything you've learned come together," says Kyndall Tatum.
Each team designs a process for the chemical depolymerization and purification of hydrocarbon polyolefin polymers. Products made from hydrocarbon polyolefins are typically used once and discarded. Most current plastic recycling methods are mechanical, not chemical. The plastic is sorted by polymer type, then melted and blended. Melt blends have less desirable mechanical properties and are used in lower-value applications for which there are limited markets.
Chemical recycling via depolymerization offers a possible solution. Chemically reversing the polymerization reaction regenerates monomers that can be purified and used in higher-value products.
Ana Inés Torres brought the circular economy approach from her research to the course. Student teams choose a specific polyolefin and work toward the goal of maximizing polyolefin recovery and minimizing the breakeven price while maintaining fitness for use specifications and reducing carbon emissions.
"Design for me is not just a process of trying to get B from A, but more a process of meeting many criteria, being mindful of sustainability and the systems around us, and weighing the costs. It's a very intricate matter," says Cindy Jiang.
Fluidized bed process design
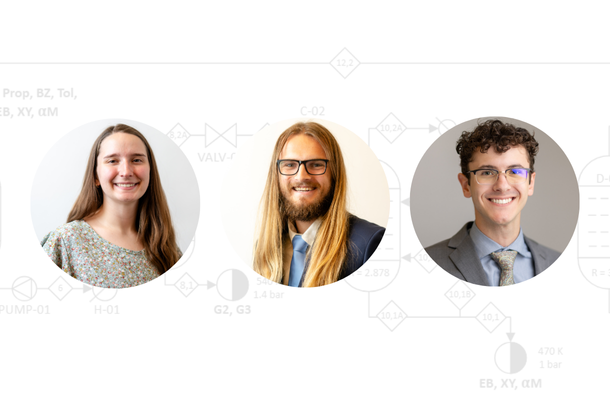
Each team begins with a literature review to select a plastic and a depolymerization approach. Ethan Cooper, Nik Firestone, and Abby Umscheid chose polystyrene, which is used in rigid molded plastic articles and foam. "We did a gross economic analysis and found that polystyrene was the most profitable and had the highest conversion in the literature," says Cooper.
Once they decided on a reaction, Cooper, Firestone, and Umscheid built out the pre-processing, or separation. To determine the expected preliminary products, they analytically solved mass and energy balances. Firestone drew on programming skills he learned in previous chemical engineering and computer science courses. He wrote Python code so that if a variable changed, he could simply update the code and run it again, rather than hand-solving hundreds of equations over and over.
Their design starts with a fluidized bed reactor to turn the polystyrene into styrene and other hydrocarbons. They then send the styrene through several separation systems, including two flash tanks and two distillation columns, to get to the required 99.8% purity.
Each team must diagram the flow of materials and energy through their process in a flowsheet. Students learn to use the modeling software Aspen Plus to implement their mass and energy balances into the reaction that they design. "It gives us a means to make our flowsheet come to life: this feed line goes to this reactor goes to this flash tank goes to this distillation column," says Umscheid.
Many of the processes within Cooper, Firestone, and Umscheid's design happen at different temperatures, and there is a large network of heat exchangers to change the temperature between each step. The team used Aspen Energy Analyzer to configure the heat exchangers to work together, reducing the energy of their overall design.
Comprehensive analysis for energy consumption and process flows is part of the final stage of the project, along with costing, economic analysis, environmental impact analysis, and a safety overview.
Cooper, Firestone, and Umscheid, like many of the teams, found that their profit would be negative for a 15 year plant life. Rather than stop with the conclusion that depolymerizing plastic isn't economically viable, "we thought about how to expand on that," says Umscheid.
"Not every new technology starts as profitable," says Firestone. "If we put a lot more into it, we can get a lot more out of it." During their economic analysis, they reexamined their settings in Aspen Plus. Running a system a degree or two cooler, for example, might save energy costs and make the whole process cheaper.
The group expects that more research would allay environmental concerns and identify opportunities to increase the profit margin for chemical recycling. "These processes aren't currently valued as they should be," says Cooper.
Steam cracking process design
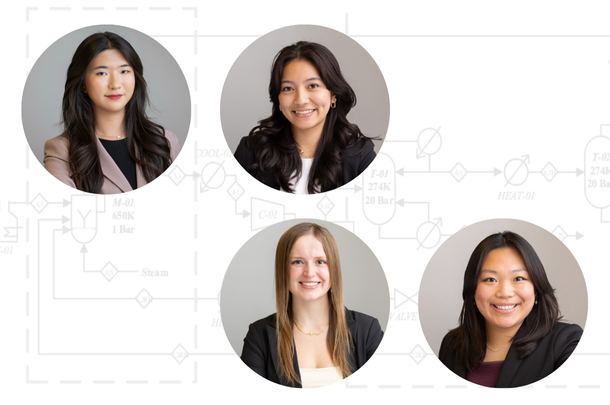
Jiang, Tatum, and their teammates Kyrsten Denise Rioveros and Krystal Xiao-Rao designed a process to recycle high density polyethylene (HDPE) using steam cracking. Because it is both firm and flexible, HDPE is one of the most commonly used plastics and can be found in products like opaque milk and detergent containers.
Their process begins with a pre-treatment in which HDPE is washed and pulverized into smaller pieces. Steam cracking uses high temperatures and steam to break down the larger polymers, resulting in ethylene and some byproducts. The final step of their process is distillation. Jiang, Rioveros, Tatum, and Xiao-Rao chose to separate the components by volatility. In a distillation column, the lighter components rise to the top, and the heavier components, in this case ethylene, stay at the bottom. With three distillation columns, they were able to get 99.9% purity, which is polymer-grade ethylene. Jiang, Rioveros, Tatum, and Xiao-Rao then recycle the byproducts back to the steam cracker to further break them down into ethylene and increase the yield.
With Aspen Plus, they simulated how their design would work in practice, and they performed a sensitivity analysis to see how they could optimize their system by changing parameters in their flowsheet. They also used the tool Greenscope, developed by the US Environmental Protection Agency, to assess their carbon emissions and environmental impact.
"If we were to continue on this project, we would start nitpicking at things to reduce costs, or find a way to increase efficiency," says Rioveros. "I think it's a really great way to get our gears turning as we prepare to enter industry or grad school. We have this special skill of not only knowing how something works but also how to design it in a way that will make it work the best."
Practical career preparation flows from a theoretical design
Chemical engineering seniors are pursuing a variety of careers, from biomedical technology and business to more traditional chemical engineering fields. The exercise of designing a process from beginning to end is relevant across them all. In Chemical Process Systems Design, seniors have opportunities to build skills researching, comparing, simulating, costing, and presenting to industrial partners. "I left this course feeling more like an engineer than I ever have," says Tatum. "I feel prepared to go into a workplace and say, 'I have these skills, and I can apply these models to problems.'"
Rioveros adds, "I don't think I could have found this experience anywhere else with any other major."
For media inquiries, please contact Lauren Smith at lsmith2@andrew.cmu.edu.