A family approach to transforming the chemical process industry
Lauren Smith
Sep 13, 2024
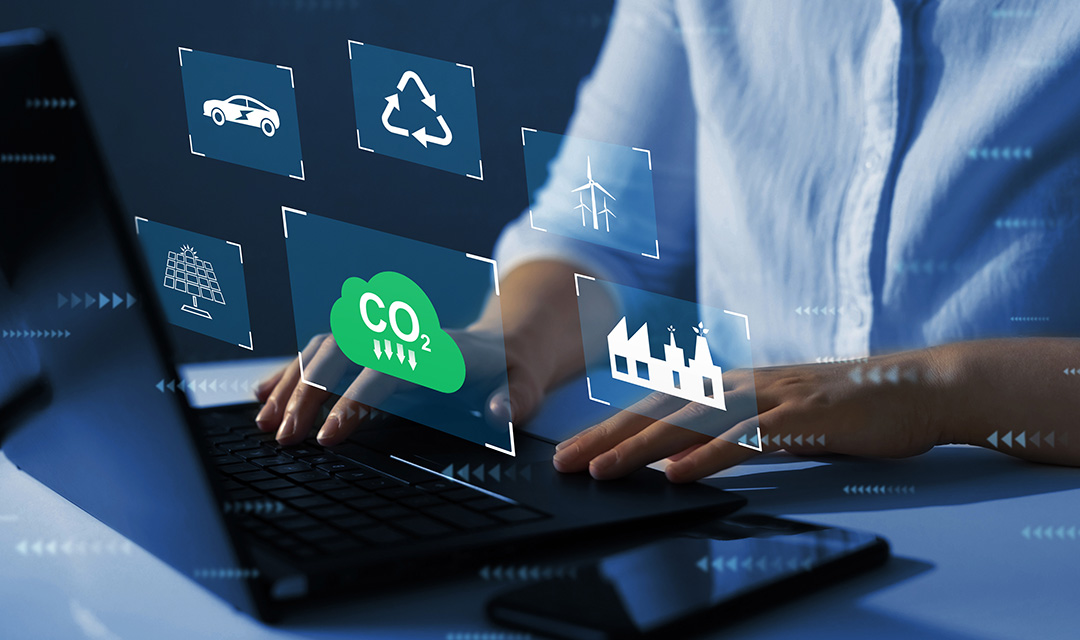
To meet climate change goals, we need to rapidly develop and broadly deploy new technologies that will transform the chemical process industry. Conventional process design approaches are too slow and too expensive.
Research from Carl Laird and Georgia Stinchfield offers a solution inspired by a product development approach long-used in the automotive industry: product family design.
"With product family design, you simultaneously consider a large number of product variants that target different customer needs while exploiting opportunities for sharing common components across these products," explains Laird, a professor of chemical engineering.
An automotive company may sell 20 different sedans, for example, yet those 20 sedans share one common frame and only two different styles of steering wheel.
Laird and Stinchfield, along with their collaborators, are advancing the area of product family design and adapting these ideas for chemical process development.
While conventional process design approaches treat each new installation independently, process family design reduces engineering design costs, standardizes manufacturing, and decreases time to market, while still providing enough variety for deployment in different use cases.
Laird and Stinchfield, a Ph.D. student, propose an optimization-based approach that simultaneously determines the optimal platform, or catalog of shared components, and designs a family of processes that use those components.
They presented their work, "Optimization of Process Families for Deployment of Carbon Capture Processes using Machine Learning Surrogates," at the 33rd European Symposium on Computer-Aided Process Engineering (ESCAPE 33) in June 2023. Together with collaborators Bashar Ammari, Joshua Morgan, John Siirola, and Miguel Zamarripa, they received the Best Oral Presentation award.
We need to deploy thousands and thousands of carbon capture processes for a variety of use cases. Uniquely designing every one of those installations is not going to be efficient economically or for deployment.
Carl Laird, Professor, Chemical Engineering
The process family approach is particularly beneficial when we need to deploy a large number of chemical processes to meet a goal, as is the case for green energy and decarbonization.
"We need to deploy thousands and thousands of carbon capture processes across the nation for a variety of different use cases, and it does not make sense to use the traditional chemical engineering approach where every one of those installations would be designed uniquely," says Laird. "That's not going to be efficient economically or for deployment."
In one case study, Laird and Stinchfield designed a family of 63 process variants for a range of solvent-based carbon capture systems. They designated two common parts in the system architecture, the regenerator and the absorber. Each process had different carbon dioxide concentrations and flow rates associated with the gas into the system.
A conventional design approach would require 63 unique regenerators and 63 unique absorbers for the 63 process variants. Using a process family design approach, Laird and Stinchfield were able to design all 63 variants using only three unique regenerators and three unique absorbers, saving on engineering design costs and opening the door for manufacturing standardization.
To solve these optimization problems, Stinchfield is using a specific type of optimization called mixed-integer linear programming (MILP). MILP was pioneered for use in chemical engineering by Ignacio Grossmann in Carnegie Mellon's Department of Chemical Engineering. The process systems group at Carnegie Mellon frequently tackles engineering challenges using advances in operations research. Here, Stinchfield was able to map her optimization problem to the P-median problem, a classic problem in operations research, for which efficient computational strategies are available.
"In current work, we are advancing our ideas to address national scale challenges and solve very large versions of the problem. We are using what I learned during my summer at Livermore to make the problem scalable," says Stinchfield, referring to a summer internship at Lawrence Livermore National Laboratory. There, she learned decomposition techniques that she and Laird have adapted to further their research and solve large-scale process family design problems.
Collaborators include:
- Joshua C. Morgan, National Energy Technology Laboratory (NETL)
- Sakshi Naik, Department of Chemical Engineering, Carnegie Mellon University
- Lorenz Biegler, Department of Chemical Engineering, Carnegie Mellon University
- John C. Eslick, NETL
- David C. Miller, NETL support contractor
- John D. Siirola, Sandia National Laboratories
- Miguel Zamarripa, NETL
- Qi Zhang, Department of Chemical Engineering and Material Science, University of Minnesota
For media inquiries, please contact Lauren Smith at lsmith2@andrew.cmu.edu.