Waveform design improves catalyst performance
Lauren Smith
Jul 18, 2024
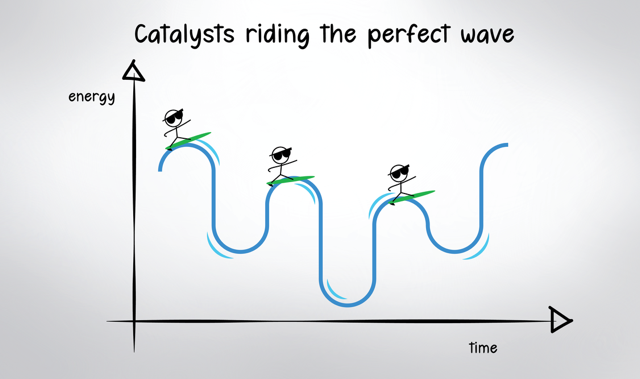
By speeding up chemical processes, catalysts enable industries to increase production, reduce waste, and decrease the size of chemical plants. Yet under the standard approach of operating chemical reactions in a steady state, known as static catalysis, there is a limit to catalyst performance.
The introduction of dynamic catalysis several years ago showed a way to beat the static limit. It offers a possible path to better-performing and lower-cost catalysts for more sustainable production.
New research from Carnegie Mellon University makes the potential of dynamic catalysis more evident.
In The Journal of Physical Chemistry C, Carolina Colombo Tedesco, John Kitchin, and Carl Laird show proof of concept for methods to simulate and optimize dynamic catalysis. Operating above the static limit requires the right conditions and the right way to oscillate material properties. The researchers developed strategies and methodologies to understand the behavior of dynamic catalytic systems.
Dynamic catalysis aims to improve catalyst performance by periodically changing, or oscillating, the properties of a material so that it behaves like a different material. "We are talking about the microscale of changing the energy between atoms. It can be hard to think on such a small scale," says Colombo Tedesco, a chemical engineering Ph.D. student. Modeling reactions helps scientists understand how they behave and how oscillating the properties can speed up the reactions.
Scientists have typically modeled dynamic catalysis by setting up a system of differential equations. "Knowing the rate at which something changes, you start at an initial value and you integrate forward in time until reaching cyclic steady state, where the behavior is oscillating in a repeatable pattern," explains Kitchin, professor of chemical engineering. It's a difficult and computationally expensive way to solve the problem.
Colombo Tedesco, Kitchin, and Laird took a different mathematical approach, solving for only one cycle, without the long integration step. Their mathematical framework makes the simulation faster and reliable, with orders-of-magnitude improvements in computational efficiency. It is also simpler to understand and implement than existing methods, and their work is completely open source. "The code to obtain the results is available in a set of Jupyter notebooks, which make the results easily reproducible," says Colombo Tedesco.
Their modeling approach also demonstrates how to optimize simultaneously. The researchers wanted to know which waveform of the oscillations provides the highest reaction rates. "There are various wave shapes, like sine, triangle, and square. We wanted to find the ideal parameters of each one of the shapes and design the best waveform," says Colombo Tedesco. They found that optimizing the oscillations increases the reaction rate more than arbitrary oscillations.
"Not only can we, given a waveform, solve for what the turnover frequency is, but we can also treat that waveform as variable and then optimize it to get the highest activity possible. That was not a convenient thing to do with other methods," says Kitchin. Having this mathematical framework is important because changing the chemical reaction, the catalyst, the reactor, or the reactive properties also changes the ideal waveform.
The researchers are now working to model a system with more reaction steps and species. To show the potential in applying their ideas experimentally and ultimately industrially, they will look at a complex system with a product that could be used for a more sustainable future.
For media inquiries, please contact Lauren Smith at lsmith2@andrew.cmu.edu.